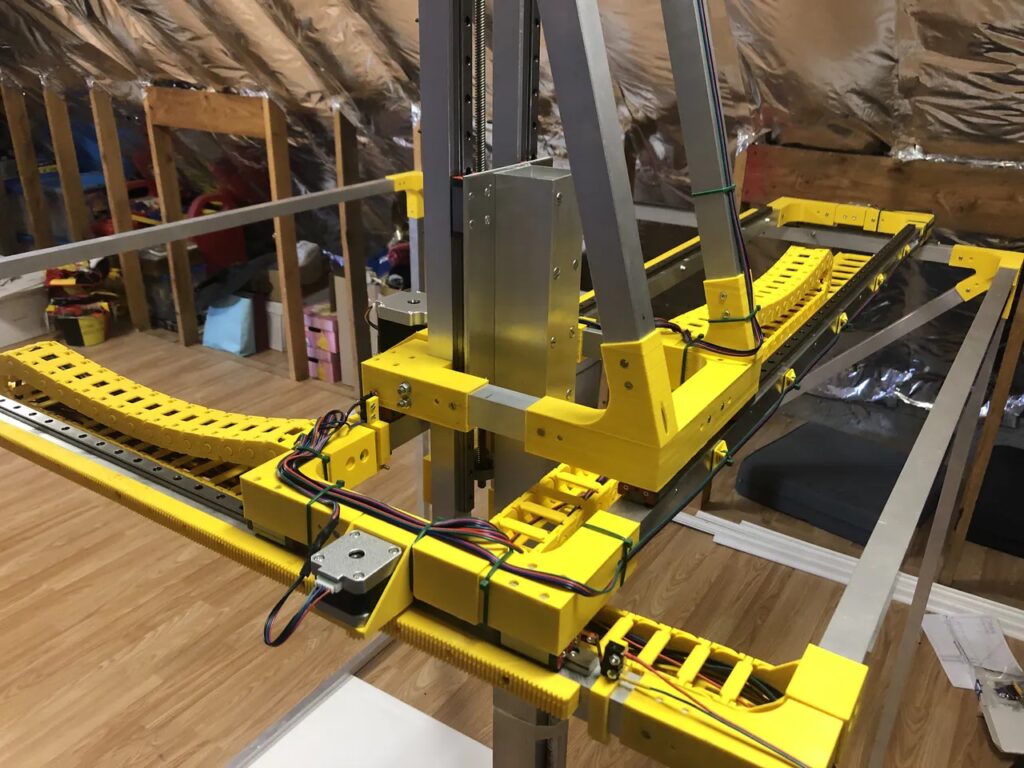
CNC (Computer Numerical Control) mills, routers, and lathes are indispensable manufacturing tools. If you need a part that adheres to tight tolerances, you turn to a CNC machine. Industrial CNC equipment is usually large, heavy, and very expensive. But small models exist for light-duty hobby jobs. This DIY version designed by Brian Brocken stands out because it is huge, has five axes, and is 3D-printable.
The most basic CNC mills and routers have three axes, so they move in the X, Y, and Z directions. But additional axes help a machine perform more complex operations. A fourth axis most often rotates the work piece, while a fifth axis tilts the spindle that rotates the end mill. It is rare to see a DIY CNC machine with five axes, but Brocken pulled it off with this project that has a massive work area of one square meter.
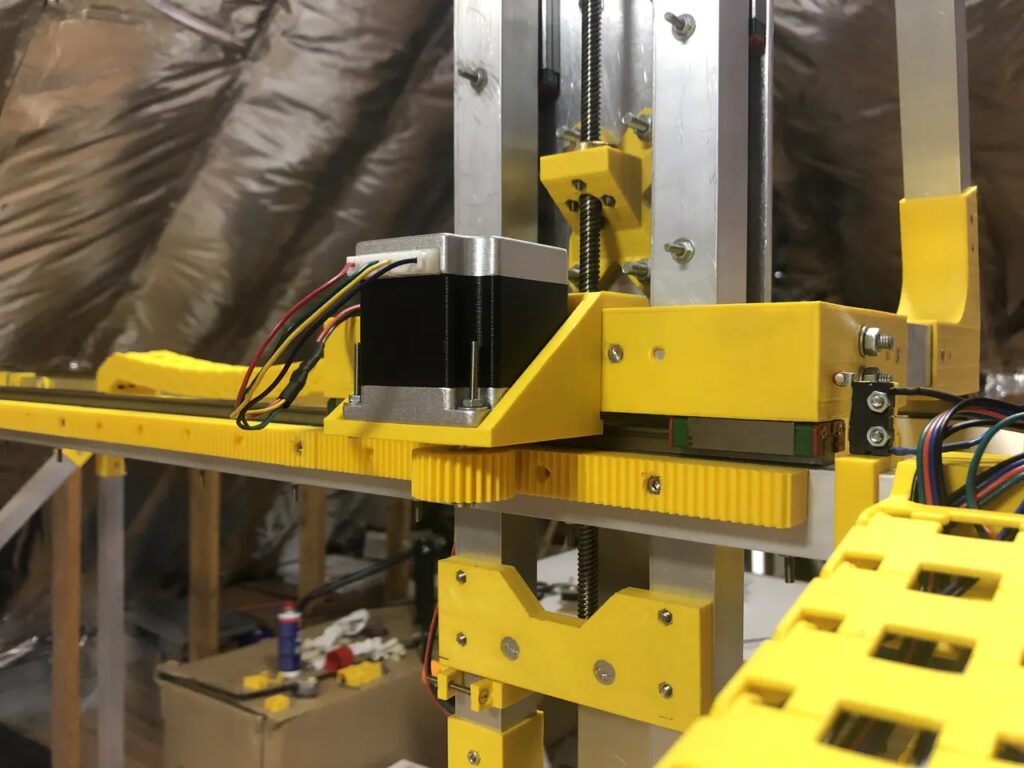
Brocken performed all the design work within Autodesk Fusion 360. The frame of the machine is aluminum tubing and 3D-printed parts. An Arduino Mega board controls the stepper motors through a RAMPS 1.4 board. It accepts standard G-code, so Brocken can create toolpaths in Fusion 360 or other CAM (Computer-Aided Manufacturing) software. The frame lacks rigidity and there is no way it could handle milling aluminum or even wood. But it can mill foam, which is the intended purpose. It can also perform 3D printing and laser cutting. Brocken isn’t quite finished building his CNC machine, but it is already semi-operational.
The post This massive five-axis CNC machine is 3D-printable appeared first on Arduino Blog.
No comments:
Post a Comment